In 1957, the Russians launched Sputnik 1, which was no more than a metal ball containing a radio, a battery, and a thermometer.[i] However, this experiment provoked a spark that led to decades of space missions. The earliest satellite designs were huge, heavy, and functionality was limited. Nevertheless, satellite designs started evolving with the passage of time and a new era of satellite modeling began with the invention of microcontrollers (MCUs). Engineers were able to reduce complex circuitry to a few parts as MCUs integrated multiple components, reduced power consumption, and minimized overall housing size and weight as Printed Circuit Board (PCB) size shrank, too. The latest development to making space accessible is the CubeSat.
What are CubeSats?
According to CubeSat101, Basic Concepts and Processes for First-Time CubeSat Developers, “CubeSats began as a collaborative effort in 1999 between Jordi Puig-Suari, a professor at California Polytechnic State University (Cal Poly), and Bob Twiggs, a professor at Stanford University’s Space Systems Development Laboratory (SSDL).” The publication by the NASA CubeSat Launch Initiative goes on to state, “The original intent of the project was to provide affordable access to space for the university science community, and it has successfully done so.”[ii]
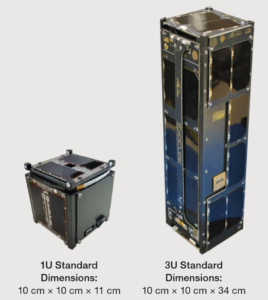
CubeSats are defined in sizes based on a standard CubeSat unit (U). A “1U” CubeSat is 10 cm3 and weighs around 1 to 1-1/3 kilograms. Since the first CubeSat, larger sizes have evolved and are based on the original 1U size, varying in size as 1.5U, 2U, 3U, and 6U, with new CubeSat sizes always a possibility. Today, many of the National Aeronautics and Space Administration’s (NASA) CubeSats contain ARM, Atmel, Texas Instruments’ MSP430, and Microchip Technology PIC microcontrollers.[iii] There are many challenges to designing electronics for aerospace or space travel, however.
Temperature, vibration, and radiation challenges
Designing for space is much more complicated than designing for standard electronics. Electronics for military, avionics, and aerospace are crafted to withstand the extreme temperatures, vibration, shock, and radiation effects commonly encountered at lift-off and outside the earth’s atmosphere. Temperatures vary along a wide range from -55°C to +125°C in space.[iv] For instance, the surface temperature of the Moon ranges from between approximately –200°C to +200°C. A satellite can be exposed to below-freezing temperatures and extremely hot temperatures within a short period of time, taxing all materials.
Extreme temperature not only shortens the life of a component, but it also affects its everyday operational functionality. Casual electronic components cannot bear such temperatures or such a wide range of temperatures for long. Commercial off-the-shelf (COTS) components that are designed to withstand the required temperature range must be used.
An electronic part or kit that is specifically designed to a level of performance and reliability may be subject to assurance processes within the industry’s supply chain. The processes are meant to establish a quality and reliability foundation for the electrical, electronic, and electromechanical components that end up in the industry’s critical applications. “These assurance processes, with inspections and tests possibly performed on a sample basis depending on criticality, are intended to identify defects and abnormalities that serve as warning signs of a potential for premature failure, reduced performance, and safety.[v] One example of an industry that conducts assurance processes is the Automotive Electronics Council, or AEC. The AEC “was originally established by Chrysler, Ford, and GM for the purpose of establishing common part-qualification and quality-system standards,” per the AEC’s site at aecouncil.com.[vi]
Components meant for space travel also have exacting standards. Temperature isn’t the only factor. Vibration at lift-off could mean the sudden application of 9.2 million pounds of thrust. The galactic cosmic rays in space pose another major challenge and are a “slowly varying, highly energetic background source of energetic particles that constantly bombard Earth,” per the National Oceanic and Atmospheric Administration (NOAA).The rays carry high-energy ions which are capable of energizing satellites electronics, resulting in malfunctioning and damages.[vii]
Galactic cosmic rays (GCR) consist of heavy elements with high energy ions and no electrons. GCRs are concentrated with protons; they lose their electrons in the course of traveling through the galaxy at the speed of light. (See Figure 2 for more information.) GRCs can pass through a satellite or an astronaut’s skin.[viii] Satellites orbiting at low altitude are more affected by radiation.[ix] In order to protect electronic components from radiation, the components must be radiation hardened.
The vacuum of outer space is also a good environment for tin whiskers to form. Pure zinc, tin, and cadmium plating are not allowed on components that qualify for existence in space.[xi]
Limited power and housing dimensions
Satellites are designed to remain in space for months or years and must have access to power. Solar power is the most likely source of energy to be used in space. The typical CubeSat is equipped with solar cells, however generating power with only a few cells means that the power supply is limited. Under these circumstances, large or power-hungry circuits are not easy to justify. Power consumption and size requirements can be reduced by using Integrated Circuits (ICs). One IC can achieve what was once achieved with a PCB covered with components. The advent of ICs contributed greatly to mankind’s capability in space.
Compatibility with available power lines
It’s possible that different ICs will require different voltage levels in a satellite. Separate voltage busses might power ICs with different voltage demands. In some cases, it is not practical to use low voltage levels as the voltages could drop significantly enough at the end of a bus to adversely affect operation. In such cases, choosing components with similar voltage level requirements might be preferable. By paying attention to the operating voltage levels of various ICs and components, designs avoid the need to provide several different power supply levels and corresponding voltage regulators. Using components with similar voltage level requirements reduces cost and energy dissipation. [xii]
Redundant systems
A typical satellite mission lasts for years, and repairs are uneconomical. Occasionally a member at the International Space Station or other entity might attempt to fix an issue, however this is a dangerous feat. Therefore, it’s essential to endeavor for flawless designs that are going to function throughout a satellite’s mission life without any issues.
For critical missions, redundant systems are often installed in case a part or system malfunctions or dies. Thus, if something fails to operate properly, the redundant system can be implemented either automatically or deployed via radio signal from earth. Interestingly, a side-effect of designing for operation in space is the flexibility of being able to continue a mission even after disconnecting primary systems.
Telemetry for monitoring all units
Although satellite designs are finalized after extensive design reviews, detailed analyses, and multiple test procedures, unfortunate circumstances may still occur. It is essential to keep track of the various voltage, current, and temperature levels of all the major components. For that, data must be transmitted from the satellite to monitoring stations on earth. Automated, remote monitoring is called telemetry. If satellite telemetry records any significant abnormalities, the associated unit may be disconnected immediately to avoid damage to other systems.
Designing systems for space used to be a government-only effort. Today, companies like SpaceX are launching satellites from earth for commercial companies and nations alike.
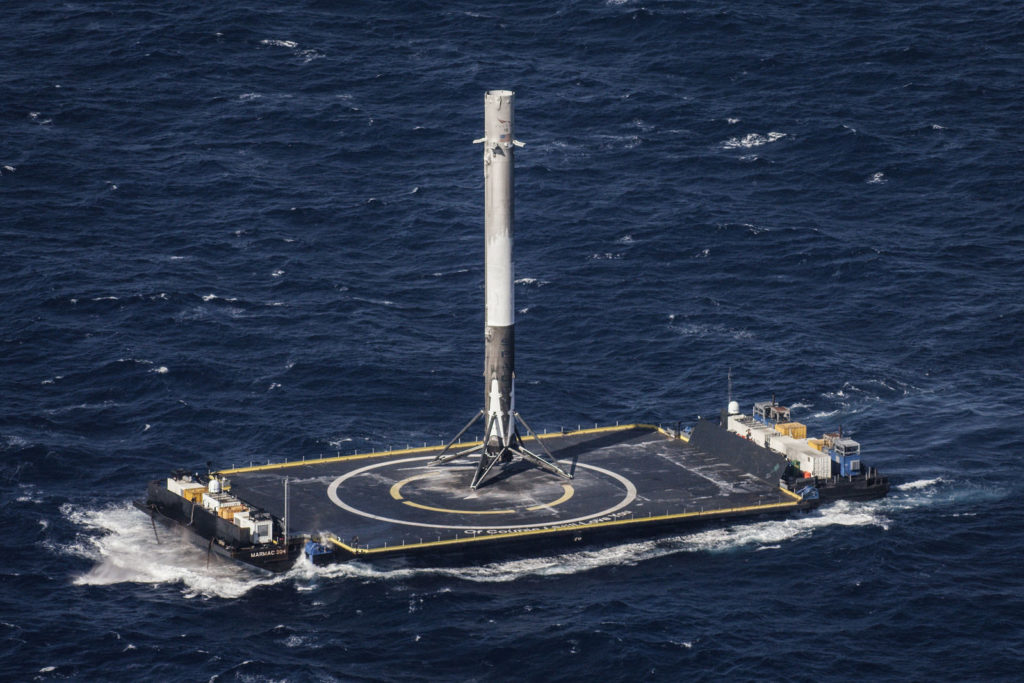
SpaceX is known for lower-cost launches and creating and successfully using the first re-useable rocket. (See Figure 3). CubeSats are a starting point for anyone who is interested in a career in space. Find out more about how to get started in CubeSats with NASA’s PDF on CubeSat technology for first-time CubeSat developers: CubeSat 101.
References:
[i] https://www.nasa.gov/missions/science/f-satellites.html
[ii] https://www.nasa.gov/sites/default/files/atoms/files/nasa_csli_cubesat_101_508.pdf
[iii] https://nepp.nasa.gov/workshops/eeesmallmissions/talks/11%20-%20THUR/1350%20-%20CubesatMicroprocessor_V1.pdf
[iv] https://www.baesystems.com/en-us/our-company/inc-businesses/electronic-systems/product-sites/space-products-and-processing/about-space-products-and-processing
[v] https://www.nasa.gov/sites/default/files/atoms/files/cots.pdf
[vi] http://www.aecouncil.com/
[vii] https://www.swpc.noaa.gov/phenomena/galactic-cosmic-rays
[viii] https://go.nasa.gov/2A474ER
[ix] https://go.nasa.gov/2A474ER
[x] https://www.nasa.gov/mission_pages/msl/multimedia/pia16938.html
[xi] https://www.analog.com/media/en/technical-documentation/tech-articles/Challenges-for-Electronic-Circuits-in-Space-Applications.pdf
[xii] https://digitalcommons.usu.edu/cgi/viewcontent.cgi?article=2070&context=etd
Thanks